機械加工で平面を削る場合、一般的には丸いモノは旋盤で加工し、その他はフライスで加工します。
最近では 6F (四角の6面体の全てがフライス加工)の材料を扱う業者さんが増えたこともあり、それを注文することが多くなりました。マシンバイスなどで6面体に加工する機会も減ってきていますね。
しかし、特殊素材、製缶品、鋳造品など正面フライスを必要とする場面はまだまだ多く存在しています。旋削の場合は連続切削で条件的に良いですが、フライス加工の場合は断続切削となり、条件が悪くなります。したがって、工具の構造や切削方法の基本を抑えて加工する必要があります。
そこで今回は正面フライス工具の使い方を説明したいと思います。
- 正面フライスの工具寿命を延ばしたい。
- 切削速度を上げたい。
そんなことを考えている人のために機械加工歴20年のセドヤが丁寧に説明します。
この記事を最後まで読むと、正面フライスの切削条件の決め方が理解でき、加工条件に合った正面フライスを選ぶことができるようになります。
※「正面削り」というと旋削も含む広い意味になるため、この記事では正面フライスで統一します。
正面フライスとは
正面フライスとは、フライス工具を使って半径方向に切込みながら切削していく工具で、広い平面の範囲を効率的に加工するための工具です。工具径はΦ50 ~φ250くらいが一般的で、メーカーにより特殊なサイズもあります。直径の大きい工具ほど効率的ですが、工作機械や、ワーク(被削材)に合わせた工具選びが大切です。
正面フライスの他に、ファイスミル、フルバック、カッターなど呼ばれます。スローアウェイタイプの正面フライスが主流で、汎用的にワークの材質や切削強度でチップ(インサート)を使い分けたり、効率を求め特定の材質専用の正面フライスもあります。また、仕上げ用のワイパーインサートをつけて、面粗度を上げることができるタイプが多く販売されています。
正面フライス工具の切れ刃について
正面フライスの切れ刃について画像で確認してください。
参照:正面フライス切れ刃諸角度/基本刃形|三菱マテリアル株式会社
図を見ると何となく創造できると思いますが、アキシャルレーキ角、ラジアルレーキ角、切込み角で真のすくい角と切れ刃傾き角が計算できます。
- 真のすくい角 tanT=tan(GAMF)×cos(KAPR)+tan(GAMP)×sin(KAPR)
- 切れ刃傾き角 tan I=tan(GAMP)×cos(KAPR)-tan(GAMF)×sin(KAPR)
アキシャルレーキ角、ラジアルレーキ角、切込み角は工具のカタログに書いてあるとこも多いですが、メーカーにより記号は異なります。例としてはアキシャルレーキは「A.R.」ラジアルレーキは「R.R.」の記号が使われることが多いです。(日立、京セラなど)
参照:正面フライス切れ刃諸角度/基本刃形|三菱マテリアル株式会社
両面使用のインサートはランニングコストに優れているが切れ味では片面使用タイプに劣ります。
柄付きタイプとアーバータイプ
正面フライス工具には柄付きタイプとアーバータイプがあります。
- 柄付きタイプは小径のモノが多く、工具の剛性は落ちますが、ホルダーで工具の長さの調整が簡単で、汎用的に使いやすいです。
- アーバータイプは工具ボディの中心に穴が開いていてアーバーと呼ばれる凸形のツールに取り付け付けて使います。柄付きに比べて重切削が可能です。通常はこちらをお勧めします。
正面フライスの切込み角
正面フライスの切込み角は切削抵抗、送り速度、工具寿命に大きな影響を与える重要な要素です。
90°、45°、10°の3つの切込み角を例に特徴を説明します。
- 90°の正面フライスは背分力(軸方向の負荷)が低くなります。しかし、正面フライスで使う場合は送り量が小さく、工具寿命も短くなる傾向があります。
- 45°の切込み角は最も安定感があります。負荷がバランスよく分散されます。
- 10°の切込み角は背分力が大きいくなります。工具の長さが必要な場合、びびりの抑制に有効です。刃先の強度も高く、送り量は大きくとれますが、軸方向の切込み量は小さくなります。
通常の正面フライス加工は45°の切込み角のモノがお勧めです。薄い板の場合は背分力を抑えるため切込み角が90°に近いモノを選ぶと「びびり」の抑制効果があります。長い工具の場合は背分力には強いので切れ刃角の小さい高送り用を使うと効率的です。
びびりについての記事はこちら⇓
機械加工の「びびり」の原因と対策
切込み角による送り量の決め方
「送り量は切りくずの厚さで決める」
私が昔、工具屋さんに教えてもらった言葉です。最初は全く意味がわからなかったので、少し説明させていただきます。
下の図で一刃あたりの送り量を0.1mmとしたときの切込み角による切りくずの厚さの変化を説明します。
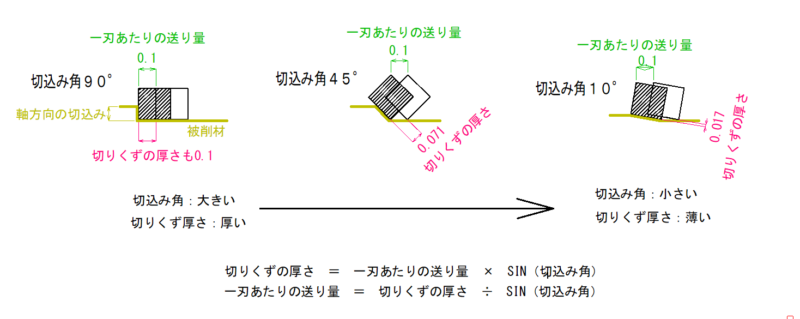
送り量が一定で切込み角が小さくなると
- 切りくずの厚さは薄くなる。(送り量を長くできる)
- 切りくずの幅は長くなる。(軸方向の切込み量は小さくなる。)
切りくずの厚さ
一刃あたりの送り量を0.1mmにしたときの切りくず厚さ。
切込み角 | 一刃0.1mmで送ったときの 切りくず厚さ(mm) |
---|---|
90° | 0.1 |
45° | 0.071 |
10° | 0.017 |
今度は切りくず厚さを0.1mmになるときの一刃あたりの送り量。
切込み角 | 切りくず厚さを0.1mmになるときの 一刃あたりの送り量(mm) |
---|---|
90° | 0.1 |
45° | 0.141 |
10° | 0.576 |
つまり、切りくずの厚さを一定にするには、計算上で90°を基準に、45°で約1.4倍、10°で約5.7倍の送り量になることがわかります。
これが「送り量は切りくずの厚さで決める」の意味です。
切りくずの幅
今度は切りくずの幅について説明します。切りくずの幅は切込み量の参考にします。
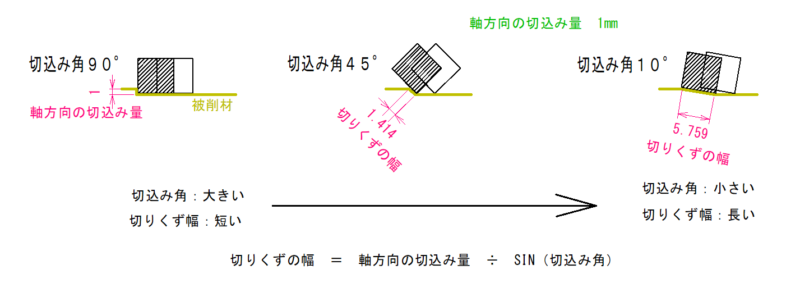
切込み角 | 軸方向の切込み量を1mmとしたときの 切りくずの幅(mm) | 切りくずの幅を1mmとしたときの 軸方向の切込み量(mm) |
---|---|---|
90° | 1 | 1 |
45° | 1.414 | 0.707 |
10° | 5.759 | 0.173 |
切りくずの幅を一定にするには、計算上で90°を基準に、45°で約0.71倍、10°で約0.17倍の軸方向の切込み量になることがわかります。
このように、軸方向の切込み量は切りくずの幅で調整します。
※もちろん機械や工具の性能、被削材により異なります。
三角関数の計算についてはこちら⇓
【三角関数】機械加工でよく使う計算方法を説明します
正面フライスの切削条件
切れ刃の数が多いほど送り速度を上げることかできますが、軸方向の切込み量は小さくなる傾向があります。
回転数や送り速度の計算についてはこちら⇓
マシニングセンターの切削条件について
切削条件に関係する工具の材質についてこちら⇓
切削工具の材質について
切削液について
インサートの材質、コーティングとの相性もあると思いますが、個人的に正面フライス加工で切削液をかけると工具寿命は短くなります。しかし、「冷却とひずみの抑制」には効果はあるので必要に応じて使い分けています。
エンゲージ角とディスエンゲージ角
エンゲージ角とは正面フライスで刃先が被削材に食付く削り始めの角度のことで、ディスエンゲージ角は刃先が抜ける削り終わりの角度のことです。これを繰り返しすのでフライスが断続切削となるわけです。
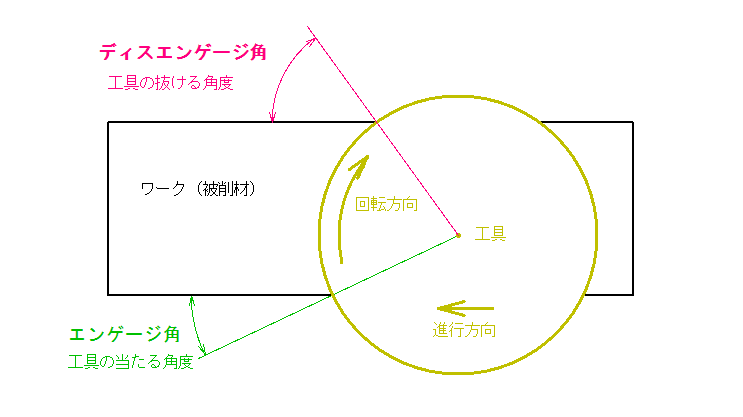
エンゲージ角とディスエンゲージ角は工具寿命に大きく影響します。エンゲージ角が小さく、ディスエンゲージ角は大きくなるような工具経路が望ましくなります。
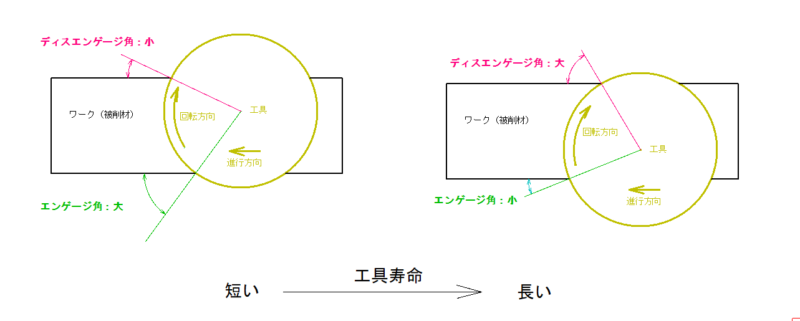
ほとんどの工具がダウンカットを推奨するのはディスエンゲージ角が大きくなり工具寿命が延びるためです。
ダウンカットとアップカットについてはこちら⇓
フライス工具のダウンカットとアップカットの違いについて
通常の正面フライスだと最初の削り始めはディスエンゲージ角が小さくなりますが、円弧補間でアプローチするとディスエンゲージ角を大きく保つことができます。

円弧補間でのアプローチは工具経路が長くなり、プログラミングが面倒ですが難削材など、工具寿命を延ばしたいときは有効な方法です。
円弧補間のプログラミングについてはこちら⇓
マシニングセンタ-の円弧補間プログラムの作り方
まとめ:【正面フライスの使い方】切込み角や切削条件について説明
正面フライスとは、半径方向に切り込みながら切削していく工具で、広い平面の範囲を効率的に加工するための工具です。ファイスミル、フルバック、カッターなど同じ意味で呼ばれる。
軸方向の刃の傾きをアキシャルレーキ角、径方向をラジアルレーキ角といい、切込み角は切りくずの厚さや刃先強度影響する。
切込み角は小さくなるほど切りくず厚さが薄くなり、切りくず幅は長くなる。
切りくず厚さは一刃あたりの送り量、切りくず幅は軸方向の切込み量に関係する要素になる。
エンゲージ角は刃先が被削材に食付く削り始めの角度で、ディスエンゲージ角は削り終わりの角度。
エンゲージ角は小さく、ディスエンゲージ角は大きくすると工具寿命が延びる。
いかかでしたか?
私は初心者のころは90°のフライスで何も考えずテキトーに削っていましたが、45°の正面フライスを使ったとき工具寿命と切削音の違いに気づき、その時から工具の形状に興味を持つようになりました。最近は工具の種類も豊富で何を選んでよいのか悩んでしまうことも多いですが、アキシャルレーキやラジアルレーキはカタログに記載されているメーカーも多いのでチェックして参考にしてみてください。
説明した通り、工具経路で工具寿命を延ばすこともできます。工夫していると面白くなってくると思います。この記事を参考にしていただければ幸いです。
以上で終わりです。
最後まで読んでいただきありがとうございます。